There are many websites and publications with detailed case-studies documenting the success of companies who have implemented Lean Six Sigma in their operations. Below are a few examples of some success stories.
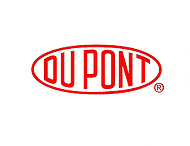
Lean Six Sigma important part of Dupont model for Sustainable Growth
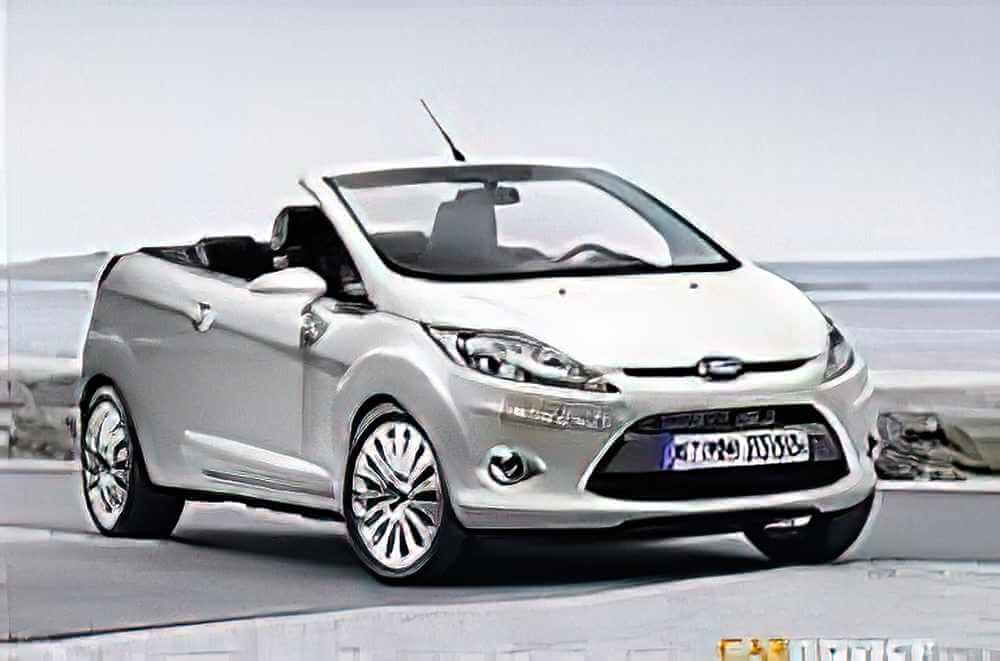
Ford Fiesta solve carpet problem with Six Sigma tool
When Ford determined that the appearance of brush marks on its 2011 Fiesta vehicle carpets would be unacceptable to customers, it decided it needed to remove the brush marks when retaining the plushness of the carpet.
A Six Sigma team used a tool called Design of Experiments (DOE) to investigate all the factors that could be the cause of the problem.
When data from 34 experimental runs was analyzed in Minitab, the results revealed complex interactions between the different settings on the equipment used to make the carpet. The interactions explained why previous adjustments to individual settings had failed to find a way to eliminate the problem. The results showed that optimization settings for eliminating brush marks did not have an adverse effect on the plushness. Incredibly, the entire project took 12 days, from the time the problem was defined to the point where the solution was in place and the process was under control.
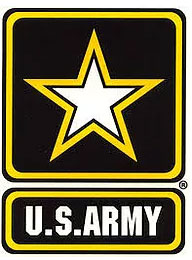
US Army increases throughput with Lean 6 Sigma program
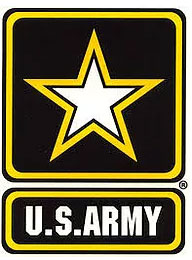
Positive Impact of lean practices on operations performance and business performance : Some evidence from Indonesian manufacturing companies
An academic research study by:
Gusman Nawanir, Lim Kong Teong and Siti Norezam Othman
School of Technology Management and Logistics,
Universiti Utara Malaysia, Sintok, Malaysia
Purpose – This study aims to investigate the relationship between lean practices, operations performance (OP), and business performance (BP). Design/methodology/approach – This survey-based studywas a cross-sectional study.The samples were drawn by using stratified random sampling procedure from large Indonesian manufacturing companies based on the directory provided by the Data and Information Center of IndonesianMinistry of Industry with the final number of respondents of 139. Four main hypotheses were developed and tested statistically by applying multivariate data analyses. Findings – The results provided evidence that lean practices should be implemented holistically. Lean practices have a positive and significant impact on both OP and BP. Moreover, OP partially mediates the relationship between lean practices and BP. Research limitations/implications – The data used in this survey represent self-reporting by mainly the middle or top management in production. Practical implications – This study contributes to the lean manufacturing (LM) body of knowledge by identifying the relationships between the LM practices, OP, and BP. Understanding these relationships will help practitioners in making better decisions in manufacturing organizations as well as enable application of the concepts in this study to other contexts such as service organizations. Originality/value – Although there are a growing number of anecdotal and empirical evidences in favor of LM in manufacturing environment, there has been almost no theory-building and methodologically rigorous research examining the link between LM, OP, and BP. This study is addressed to fill this gap.